Adjustable Thermal Expansion Properties in Zr2MoP2O12/ZrO2 Ceramic Composites
- 1Department of Microelectronics, School of Physical Science and Technology, Yangzhou University, Yangzhou, China
- 2Department of Electrical and Mechanical Engineering, Guangling College, Yangzhou University, Yangzhou, China
Zr2MoP2O12/ZrO2 composites were successfully synthesized by the solid state method in attempt to fabricate the near-zero thermal expansion ceramics. The phase composition, micromorphology and thermal expansion behavior of the Zr2MoP2O12/ZrO2 composites with different mass ratios were investigated using X-ray diffraction, scanning electron microscopy and thermal mechanical analysis. Results indicate that Zr2MoP2O12/ZrO2 composites can be prepared by pre-sintering at 500°C for 3 h and then sintering at 1050°C for 6 h. The resulting Zr2MoP2O12/ZrO2 composites consisted of orthorhombic Zr2MoP2O12 and monoclinic ZrO2. With increasing content of Zr2MoP2O12, the Zr2MoP2O12/ZrO2 ceramics became more compact and the coefficient of thermal expansion decreased gradually. Zr2MoP2O12/ZrO2 composites show an adjustable coefficient of thermal expansion (CTE) from 5.57 × 10−6 K−1 to −5.73 × 10−6 K−1 by changing the mass ratio of Zr2MoP2O12 and ZrO2. The Zr2MoP2O12/ZrO2 composite with a mass ratio of 2:1 showed near zero thermal expansion, and the average linear thermal expansion coefficient is measured to be 0.0065 × 10−6 K−1 in the temperature range from 25 to 700°C.
Introduction
It is well known that the vast majority of materials expand on heating. However, some materials shrink as the temperature rises and display negative thermal expansion (NTE). NTE materials have attracted considerable attention due to the anomalous phenomenon and their potential application in controlled thermal expansion composites and other areas (Chen et al., 2015). Control of thermal expansion is crucial to many applications. Mismatch of thermal expansion in component materials of high-precision device may result in serious problems, such as mechanical destruction and positional deviation. An easy method to prepare the material with near-zero or low thermal expansion is combining NTE materials with positive thermal expansion materials (Liu et al.2012; 2012a; Gao et al., 2016; Zhang et al., 2017). Materials displaying zero or low thermal expansion are both dimensionally stable and highly resistant to thermal shock.
The longtime leading NTE exemplar was ZrW2O8. Cubic ZrW2O8 exhibits strong isotropic NTE over a wide temperature range (Mary et al., 1996; Nishiiyama et al., 2006; Kanamori et al., 2008; Banek et al., 2010; Liu et al., 2011, 2012b). With the goal of thermal expansion control, several studies of the composites containing ZrW2O8 have been reported, such as ZrW2O8/ZrO2 (Lommens et al., 2005; Yang et al., 2007), ZrW2O8/Cu (Yilmaz, 2002), ZrW2O8/Al (Wu et al., 2013), ZrW2O8/cement (Kofteros et al., 2001), ZrW2O8/PI, and ZrW2O8/epoxy (Sullivan and Lukehart, 2005; Yang et al., 2010). The thermal expansion coefficient of composites can be effectively controlled by using ZrW2O8 as NTE filler, however, the cubic ZrW2O8 is metastable at room temperature and needs to be quenched after sintering at 1200°C. Meanwhile, ZrW2O8 undergoes a structural phase transition from α -ZrW2O8 to β -ZrW2O8 at around 160°C and the coefficient of thermal expansion will decrease from about −8.8 × 10−6 K−1 to −4.9 × 10−6 K−1. In addition, when ZrW2O8 was heated to about 740°C in air, it will decompose into ZrO2 and WO3 (Mary et al., 1996; Nishiiyama et al., 2006; Kanamori et al., 2008; Banek et al., 2010; Liu et al., 2011, 2012b). Quenching, thermal decomposition and the abrupt change of thermal expansion are disadvantageous for composite design.
Orthorhombic Zr2MoP2O12, a member of A2M3O12 family, has received widespread attention in recent years. It shows stable NTE and its average linear expansion coefficient is −4.5 × 10−6 K−1 over a broad temperature range from −264 to 1050°C. What's more, it overcomes all the limitations of ZrW2O8 discussed above, suggesting its potential use for fabricating near-zero or low thermal expansion materials (Cetinkol et al., 2009; Isobe et al., 2016). ZrO2 ceramics has been widely used in optical, electrical and high temperature fields. The average linear thermal expansion coefficient of ZrO2 is about 10 × 10−6 K−1(Lommens et al., 2005; Yang et al., 2007). The absolute values of thermal expansion coefficient of ZrO2 and Zr2MoP2O12 are thus similar but have opposite signs, suggesting that these materials are good candidates for the preparation of ceramic composites with tunable CTEs. In this work, a new series of Zr2MoP2O12/ZrO2 composites were synthesized by solid state method with the goal of tailoring the thermal expansion. The effects of mass ratio between Zr2MoP2O12 and ZrO2 on the phase composition, microstructure, and thermal expansion coefficient of the Zr2MoP2O12/ZrO2 ceramic composites were also investigated.
Experimental
Sample Preparation
Zr2MoP2O12, ZrO2, and Zr2MoP2O12/ZrO2 composites (mass ratios: 1:2, 1:1, 2:1) were prepared using stoichiometric amounts of ZrO2 (purity ≥99.95%, metals basis), MoO3 (purity ≥99.99%, metals basis), and NH4H2PO4 (purity ≥99.5%, metals basis). A summary of samples prepared can be found in Table 1. The starting compounds were mixed in ethanol using ball milling for 6 h to form a uniform mixture and dried at 80°C, then the mixtures were pre-heated at 500°C for 3 h. The mixtures, under 50 MPa, were cold pressed into pellets which were 7 mm in diameter and about 2 mm in thickness. Finally, the pellets were calcined at 1050°C in air for 6 h and cooled down in the furnace. In the solid-state synthesis, the following reactions may take place:
In this work, the 2:1 Zr2MoP2O12/ZrO2 composite was also prepared using the pure Zr2MoP2O12 and ZrO2 as raw materials, and the synthetic process is the same as that of the above process.
Experimental Techniques
Identification of the different phases presented in the samples was performed using powder X-ray diffraction (PXRD) on a Shimadzu XRD 7000 with Cu Ka radiation. Data were collected at 40 kV and 35 mA, with a scanning speed of 5°/min over an angular range of 10–60°. The micromorphologies of the samples were observed using a scanning electron microscopy (SEM, TESCAN VEGA3). The elemental composition of the samples were analyzed using energy-dispersive X-ray spectrometry (EDX, Bruker XFlash 6160) as well.The CTEs of the samples were measured by thermal mechanical analyzer (TMA/SS, Seiko 6300) using a heating rate of 5°C/min from room temperature to 700°C in air.
Results and Discussion
XRD Analysis
Figure 1 shows typical XRD patterns of the Zr2MoP2O12/ZrO2 (mass ratios 1:2, 1:1, and 2:1) composites in addition to those of the pure Zr2MoP2O12 and ZrO2 ceramics obtained under the same preparation condition. Figure 1a shows typical powder XRD pattern of pure ZrO2 ceramics sintered at 1050°C for 6 h, all the observed reflections could be well indexed and attributed to monoclinic ZrO2 in agreement with JCPDS card number 65–1,023. The typical powder XRD pattern of pure Zr2MoP2O12 specimen sintered at 1050°C for 6 h is shown in Figure 1e, all diffraction peaks match those expected for orthorhombic Zr2MoP2O12, which agrees with literature reports (Cetinkol et al., 2009; Isobe et al., 2016). No impurity phases were detected, confirming the purity of the two products. The PXRD patterns of the Zr2MoP2O12/ZrO2 (mass ratio: 1:2, 1:1, and 2:1) composites were shown in Figures 1b–d, it can be seen that all the diffraction peaks of the specimens could be indexed as both monoclinic ZrO2 and orthorhombic Zr2MoP2O12. With increasing mass ratio of Zr2MoP2O12, the intensity of diffraction peaks of Zr2MoP2O12 become much stronger. The diffraction peaks of both ZrO2 and Zr2MoP2O12 were sharp and intense, indicating their highly crystalline nature.
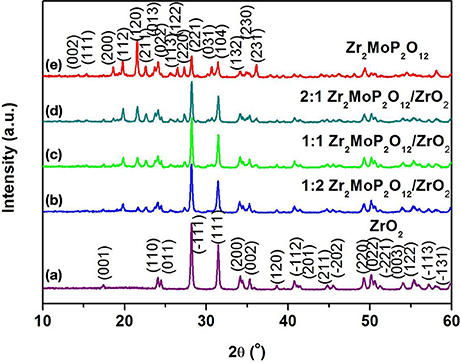
Figure 1. XRD patterns of the obtained ZrO2 ceramics, Zr2MoP2O12 ceramics and Zr2MoP2O12/ZrO2 composites with different mass ratios sintered at 1050°C for 6 h.
To investigate whether a chemical reaction occurred between ZrO2 and Zr2MoP2O12 during sintering at 1050°C. The 2:1 Zr2MoP2O12/ZrO2 composite was also prepared using the pure Zr2MoP2O12 and ZrO2 as raw materials. The Zr2MoP2O12 was mixed with ZrO2 at a mass ratio of 2:1 and finally calcined at 1050°C in air for 6 h. The XRD patterns of the ZrO2, Zr2MoP2O12, and 2:1 Zr2MoP2O12/ZrO2 were shown in Figure 2. Except for monoclinic ZrO2 and orthorhombic Zr2MoP2O12, no new peaks were detected, confirming that no chemical reaction occurred between ZrO2 and Zr2MoP2O12 during sintering at 1050°C.
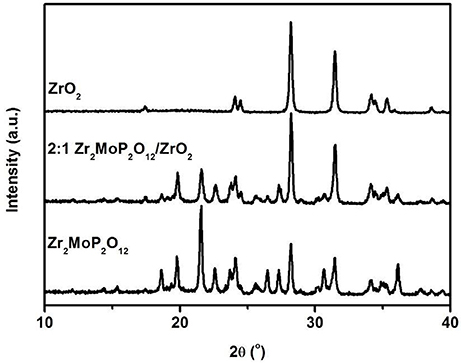
Figure 2. XRD patterns of the obtained 2:1 Zr2MoP2O12/ZrO2 composites sintered at 1050°C for 6 h using the Zr2MoP2O12 and ZrO2 as raw materials, and the XRD patterns of pure Zr2MoP2O12 and ZrO2 were also given for reference.
SEM Images and Density Analysis
Further study was carried out by the SEM analysis to identify microstructures of as-prepared Zr2MoP2O12, ZrO2, and Zr2MoP2O12/ZrO2 composites. Figure 3 shows SEM images of fracture surfaces of the pure ZrO2, pure Zr2MoP2O12 sintered bodies, and the Zr2MoP2O12/ZrO2 composites fabricated with different mass ratio of 1:2, 1:1, and 2:1. As shown in Figure 3a, as-prepared ZrO2 ceramics sintered at 1050°C is not compact and the ZrO2 grain growth is not observed obviously due to the insufficient sintering. The SEM images of the Zr2MoP2O12/ZrO2 composites fabricated at different mass ratio of 1:2, 1:1, and 2:1 are shown in Figures 3b–d. It can be seen that the Zr2MoP2O12/ZrO2 composites show nearly the same SEM images of fracture surfaces, which consist of irregular grains and some pores. With increasing content of Zr2MoP2O12, Zr2MoP2O12/ZrO2 ceramics became denser and displayed larger particle sizes and less porosity, suggesting that the increase of Zr2MoP2O12 slightly promoted the particle growth and increased the density of the Zr2MoP2O12/ZrO2 ceramics. Figure 3e shows the SEM images of fracture surfaces of the obtained pure Zr2MoP2O12 ceramics. The Zr2MoP2O12 sintered body was denser compared with the ZrO2 ceramics fabricated at same sintering temperature. It is compact, which is in agreement with the results reported earlier (Cetinkol et al., 2009; Isobe et al., 2016). The elemental composition and distribution of 2:1 Zr2MoP2O12/ZrO2 composite was also investigated using the EDX. The distribution of zirconium, oxygen, phosphorus, molybdenum is shown in Figures 3f–j.
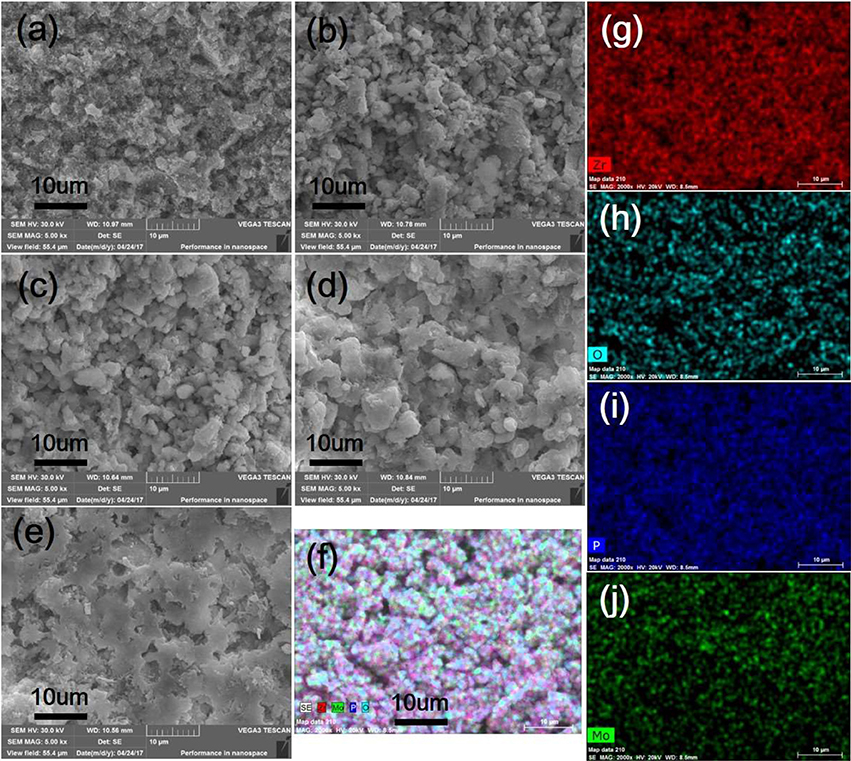
Figure 3. SEM images of the obtained ZrO2 ceramics, Zr2MoP2O12 ceramics and Zr2MoP2O12/ZrO2 composites with different mass ratios sintered at 1050°C for 6 h. (a) ZrO2 (b) Zr2MoP2O12:ZrO2 = 1:2 (c) Zr2MoP2O12:ZrO2 = 1:1 (d) Zr2MoP2O12:ZrO2 = 2:1 (e) Zr2MoP2O12 (f) overlaid with elemental analysis results of 2:1 Zr2MoP2O12/ZrO2 composite using EDX (g–j) distribution of zirconium, oxygen, phosphorus, molybdenum elements in the selected area.
Thermal Expansion Properties
For a better analysis of the thermal expansion behaviors of the composites, Figure 4A shows the thermal expansion curves of the Zr2MoP2O12/ZrO2 composites with different mass ratio calcined at 1050°C for 6 h. The thermal expansion curves of the pure Zr2MoP2O12 and pure ZrO2 ceramics are also given for reference. As shown in Figures 4A–a, Pure ZrO2 specimen shows positive thermal expansion in the testing temperature from 25 to 700°C with an average linear thermal expansion coefficient of 5.57 × 10−6 K−1, which agrees with literature reports (Lommens et al., 2005; Yang et al., 2007). In Figures 4A-e, it can be seen that pure Zr2MoP2O12 ceramics showed strong negative thermal expansion. Its average linear thermal expansion coefficient was measured to be −5.73 × 10−6 K−1 in the testing temperature range of 25–700°C. It can be found that the thermal expansion curves of the obtained samples except pure Zr2MoP2O12 ceramics overlap below 200°C, this abnormal behavior in the beginning of thermal expansion curves may be caused by the instrument. Above 200°C, all the samples show stable and almost linear change in the curves of thermal expansion with the increased temperature. Based on the above SEM analysis, the compact microstructure of the composites will promotes the stability of thermal expansion performance. Average linear thermal expansion coefficients of the obtained pure ZrO2, pure Zr2MoP2O12, and Zr2MoP2O12/ZrO2 composites with different mass ratios are summarized in Table 2. With increasing content of Zr2MoP2O12, the thermal expansion coefficient of Zr2MoP2O12/ZrO2 composite decreased gradually. The 1:2 Zr2MoP2O12/ZrO2 composite showed positive thermal expansion with a thermal expansion coefficient of 2.30 × 10−6 K−1. When the mass ratio of Zr2MoP2O12/ZrO2 decreased to 1:1, the composite also exhibited positive thermal expansion, but the CTE value decreased to 1.14 × 10−6 K−1. The 2:1 Zr2MoP2O12/ZrO2 composite showed very low thermal expansion with an average linear thermal expansion coefficient of 0.0082 × 10−6 K−1 in the temperature range of 25–700°C. Figure 4B shows the cyclic thermal expansion curves of the Zr2MoP2O12/ZrO2 composites. The two thermal expansion curves are almost the same, and the second average linear thermal expansion coefficient was test to be 0.0049 × 10−6 K−1 in the same temperature range, indicating the 2:1 Zr2MoP2O12/ZrO2 composite shows a stable thermal expansion property and the mass ratio of 2:1 (Zr2MoP2O12/ZrO2) is appropriate one. With the increase of the temperature, the volume shrinkage of the NTE Zr2MoP2O12 just can accommodate the volume expansion of ZrO2, which will keep a little change of the volume value of the 2:1 Zr2MoP2O12/ZrO2 composite. This near-zero expansion ceramic composite can withstand thermal stresses arising during sintering and subsequent quenching, which is an important criterion for a number of potential application in many fields. The results suggest that the thermal expansion coefficients of Zr2MoP2O12/ZrO2 composites can be tailored from 5.57 × 10−6 K−1 to −5.73 × 10−6 K−1 by adjusting the weight fraction of Zr2MoP2O12. Figure 5 shows the relation between coefficients of thermal expansion and the mass ratio of the Zr2MoP2O12/ZrO2 composites sintered at 1050°C for 6 h. The points is the data measured in the work. There is no linear relationship between the coefficients of thermal expansion and the mass ratio of the Zr2MoP2O12/ZrO2 composites. The red line is the best-fit line. According to the fitting equation, when the mass ration of Zr2MoP2O12/ZrO2 is 0.57, the Zr2MoP2O12/ZrO2 composite show zero thermal expansion. This fitting result deviates from the data obtained in the experiment. When the mass ration of Zr2MoP2O12/ZrO2 is 0.67, the near-zero thermal expansion Zr2MoP2O12/ZrO2 composite was obtained. This deviation mainly caused by the defects in the composites, such as pores and microcracks.
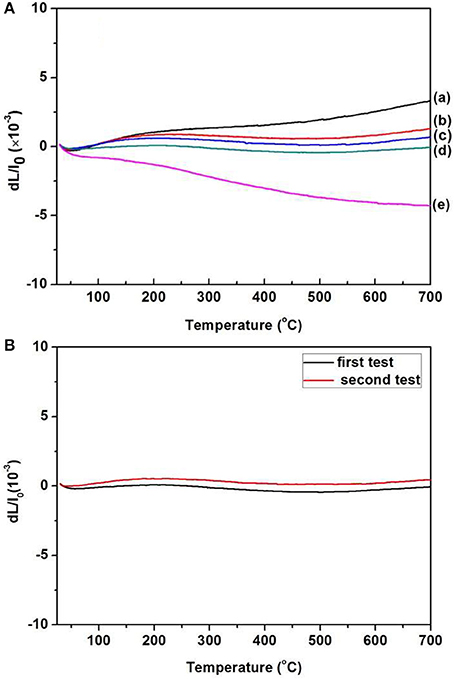
Figure 4. (A)Thermal expansion curves of the obtained ZrO2 ceramics, Zr2MoP2O12 ceramics and Zr2MoP2O12/ZrO2 composites with different mass rati006Fs sintered at 1050°C for 6 h. (a) ZrO2 (b) Zr2MoP2O12:ZrO2 = 1:2 (c) Zr2MoP2O12:ZrO2 = 1:1 (d) Zr2MoP2O12:ZrO2 = 2:1 (e) Zr2MoP2O12. (B) Cyclic thermal expansion curves of the 2:1 Zr2MoP2O12/ZrO2 composite.
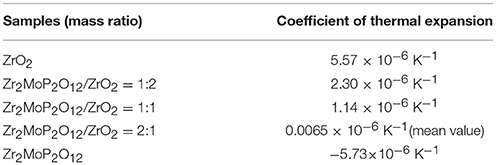
Table 2. Average linear thermal expansion coefficients of ZrO2 ceramics, Zr2MoP2O12 ceramics, and Zr2MoP2O12/ZrO2 composites with different mass ratios in corresponding testing temperature range from 25 to 700°C.
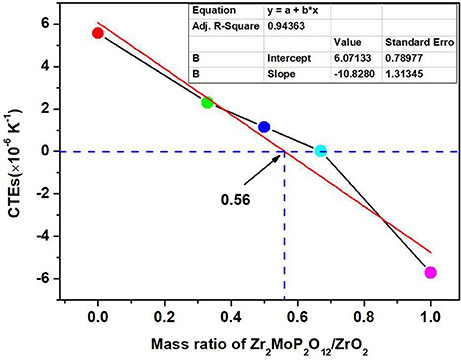
Figure 5. Relation between coefficients of thermal expansion and the mass ratio of the Zr2MoP2O12/ZrO2 composites sintered at 1050°C for 6 h.
Conclusions
With the goal of thermal expansion control, NTE Zr2MoP2O12 was combined with the positive thermal expansion ZrO2 to fabricate the composites with a tailorable thermal expansion. The obtained Zr2MoP2O12/ZrO2 composites synthesized at 1050°C for 6 h were composed of orthorhombic Zr2MoP2O12 and monoclinic ZrO2, no intermediate phase was observed. With increasing content of Zr2MoP2O12, the thermal expansion coefficient of Zr2MoP2O12/ZrO2 composite decreased while the density of the composite increased gradually. The thermal expansion coefficients of the Zr2MoP2O12/ZrO2 composites can be tailored from 5.57 × 10−6 K−1 to −5.73 × 10−6 K−1 by changing the weight fraction of Zr2MoP2O12. In addition, the 2:1 Zr2MoP2O12/ZrO2 composite displayed near-zero thermal expansion with an average linear thermal expansion coefficient of 0.0065 × 10−6 K−1 in the testing temperature range of 25–700°C. This near-zero thermal expansion material will have a number of potential application in many fields due to its dimensional stability and high resistance to thermal shock.
Author Contributions
HL and ZZ designed experiments. WS, XX, and LY carried out experiments. HL, ZZ, XZ, MZ, and XC analyzed experimental results. HL and ZZ wrote the manuscript.
Conflict of Interest Statement
The authors declare that the research was conducted in the absence of any commercial or financial relationships that could be construed as a potential conflict of interest.
Acknowledgments
The authors thank the National Natural Science Foundation of China (No.51602280 and No.51102207), Qing Lan Project of Jiangsu Province, Guangling College of Yangzhou University Natural Science Research Foundation (ZKZD17001). Yangzhou University Science and Technique Innovation Foundation (No.2015CJX007).
References
Banek, N. A., Baiz, H. I., Latigo, A., and Lind, C. (2010). Autohydration of nanosized cubic zirconium tungstate. J. Am. Chem. Soc. 132, 8278–8279. doi: 10.1021/ja101475f
Cetinkol, M., Wilkinson, A. P., and Lee, P. (2009). Structural changes accompanying negative thermal expansion in Zr2(MoO4)(PO4)2. J. Solid State Chem. 182, 1304–1311. doi: 10.1016/j.jssc.2009.02.029
Chen, J., Hu, L., Deng, J., and Xing, X. (2015). Negative thermal expansion in functional materials: controllable thermal expansion by chemical modifications. Chem. Soc. Rev. 44, 3522–3567. doi: 10.1039/C4CS00461B
Gao, X. D., Coleman, M. R., and Lind, C. (2016). Surface modification of ZrW2O8 and ZrW2O7(OH)2×2H2O filler particles for controlled thermal expansion polycarbonate composites. Pol. Comp. 37, 1359–1368. doi: 10.1002/pc.23304
Isobe, T., Houtsuki, N., Hayakawa, Y., Yoshida, K., Matsushita, S., and Nakajima, A. (2016). Preparation and properties of Zr2MoP2O12 ceramics with negative thermal expansion. Mater. Design. 112, 11–16. doi: 10.1016/j.matdes.2016.09.048
Kanamori, K., Kineri, T., Fukuda, R., Nishio, K., and Yasumori, A. (2008). Preparation and formation mechanism of ZrW2O8 by Sol–Gel process. J. Am. Ceram. Soc. 90, 3542–3545. doi: 10.1111/j.1551-2916.2008.02726.x
Kofteros, M., Rodriguez, S., and Tandon, V. (2001). A preliminary study of thermal expansion compensation in cement by ZrW2O8 additions. Scripta Mater. 45, 369–374. doi: 10.1016/S1359-6462(01)01009-0
Liu, H. F., Zhang, W., Zhang, Z. P., and Chen, X. B. (2012a). Synthesis and negative thermal expansion properties of solid solutions Yb2−−xLaxW3O12 (0 ≤ x ≤ 2). Ceram. Int. 38, 2951–2956. doi: 10.1016/j.ceramint.2011.11.072
Liu, H. F., Zhang, Z. P., Zhang, W., and Chen, X. B. (2011). Negative thermal expansion ZrW2O8 thin films prepared by pulsed laser deposition. Surf. Coat. Technol. 205, 5073–5076. doi: 10.1016/j.surfcoat.2011.05.010
Liu, H. F., Zhang, Z. P., Zhang, W., and Chen, X. B. (2012b). Effects of HCl concentration on the growth and negative thermal expansion property of the ZrW2O8 nanorods. Ceram. Int. 38, 1341–1345. doi: 10.1016/j.ceramint.2011.09.010
Liu, Q. Q., Yang, J., Cheng, X. N., Liang, G. S., and Sun, X. J. (2012). Preparation and characterization of negative thermal expansion Sc2W3O12/Cu core–shell composite. Ceram. Int. 38, 541–545. doi: 10.1016/j.ceramint.2011.07.041
Lommens, P., Meyer, C. D., Bruneel, E., Buysser, K. D., Driessche, I. V., and Hoste, S. (2005). Synthesis and thermal expansion of ZrO2/ZrW2O8 composites. J. Europ. Ceram. Soc. 25, 3605–3610. doi: 10.1016/j.jeurceramsoc.2004.09.015
Mary, T. A., Evans, J. S. O., Vogt, T., and Sleight, A. W. (1996). Negative thermal expansion from 0.3 K to 1050 K in ZrW2O8. Science 272, 90–92.
Nishiiyama, S., Hayashi, T., and Hattori, T. (2006). Synthesis of ZrW2O8 by quick cooling and measurement of negative thermal expansion of the sintered bodies. J. Alloys Compd. 417, 187–189. doi: 10.1016/j.jallcom.2005.07.075
Sullivan, L. M., and Lukehart, C. M. (2005). Zirconium tungstate (ZrW2O8)/polyimide nanocomposites exhibiting reduced coefficient of thermal expansion. Chem. Mater. 17, 2136–2141. doi: 10.1021/cm0482737
Wu, Y., Wang, M. L., Chen, Z., Ma, N. H., and Wang, H. W. (2013). The effect of phase transformation on the thermal expansion property in Al/ZrW2O8 composites. J. Mater. Sci. 48, 2928–2933. doi: 10.1007/s10853-012-6933-x
Yang, J., Yang, Y. S., Liu, Q. Q., Xu, G. F., and Cheng, X. N. (2010). Preparation of negative thermal expansion ZrW2O8 powders and its application in polyimide/ZrW2O8 composites. J. Mater. Sci. Technol. 26, 665–668. doi: 10.1016/S1005-0302(10)60103-X
Yang, X. B., Cheng, X. N., Yan, X. H., Yang, J., Fu, T. B., and Qiu, J. (2007). Synthesis of ZrO2/ZrW2O8 composites with low thermal expansion. Compos. Sci. Technol. 67, 1167–1171. doi: 10.1016/j.compscitech.2006.05.012
Yilmaz, S. (2002). Thermal mismatch stress development in Cu-ZrW2O8 composite investigated by synchrotron X-ray diffraction. Comp. Sci. Technol. 62, 1835–1839. doi: 10.1016/S0266-3538(02)00104-5
Keywords: ceramics, Zr2MoP2O12, ZrO2, composites, thermal expansion control
Citation: Liu H, Sun W, Xie X, Yang L, Zhang Z, Zhou M, Zeng X and Chen X (2018) Adjustable Thermal Expansion Properties in Zr2MoP2O12/ZrO2 Ceramic Composites. Front. Chem. 6:347. doi: 10.3389/fchem.2018.00347
Received: 02 May 2018; Accepted: 24 July 2018;
Published: 14 August 2018.
Edited by:
Jun Chen, University of Science and Technology Beijing, ChinaReviewed by:
Kewen Shi, Beihang University, ChinaSihao Deng, Southwest University of Science and Technology, China
Cristina Artini, Università di Genova, Italy
Copyright © 2018 Liu, Sun, Xie, Yang, Zhang, Zhou, Zeng and Chen. This is an open-access article distributed under the terms of the Creative Commons Attribution License (CC BY). The use, distribution or reproduction in other forums is permitted, provided the original author(s) and the copyright owner(s) are credited and that the original publication in this journal is cited, in accordance with accepted academic practice. No use, distribution or reproduction is permitted which does not comply with these terms.
*Correspondence: Zhiping Zhang, zp-hf@163.com