Permeability Enhancement Properties of High-Pressure Abrasive Water Jet Flushing and Its Application in a Soft Coal Seam
- 1School of Aeronautical Engineering, Zhengzhou University of Aeronautics, Zhengzhou, China
- 2School of Mechanical and Power Engineering, Zhengzhou University, Zhengzhou, China
- 3Department of Power Engineering and Turbomachinery, Silesian University of Technology, Gliwice, Poland
High-pressure abrasive water jet flushing (HPAWJF) is an effective method used to improve coal seam permeability. In this study, based on the theories of gas flow and coal deformation, a coupled gas-rock model is established to investigate realistic failure processes by introducing equations for the evolution of mesoscopic element damage along with coal mass deformation. Numerical simulation of the failure and pressure relief processes is carried out under different coal seam permeability and flushing length conditions. Distributions of the seepage and gas pressure fields of the realistic failure process are analyzed. The effects of flushing permeability enhancement in a soft coal seam on the gas drainage from boreholes are revealed by conducting a field experiment. Conclusions can be extracted that the gas pressure of the slotted soft coal seam is reduced and that the gas drainage volume is three times higher than that of a conventional borehole. Field tests demonstrate that the gas drainage effect of the soft coal seam is significantly improved and that tunneling speed is nearly doubled. The results obtained from this study can provide guidance to gas drainage in soft coal seams regarding the theory and practice application of the HPAWJF method.
Introduction
Coal and gas outbursts have been widely studied because of their serious threat to safety in coal mine production (Frid, 1997; Li and Hua, 2006; Cao and Bian, 2019). High-pressure abrasive water jet flushing (HPAWJF) is a rapidly developing technology used to prevent coal and gas outbursts (Jiang et al., 2009, 2011). However, the geological conditions of soft coal seams, which are widely distributed in China, are relatively complex. Notably, the permeability of the soft coal seams of China is three to four orders of magnitude lower than those of Australia and North America (Aguado and Nicieza, 2007; Cheng et al., 2011). In recent years, with the increase in excavation depth of coal mining, the features of high gas content, high geostress, high geotemperature, and low permeability of soft coal seams have been significantly increasing (Jin et al., 2015), and the increasing number of coal and gas outbursts causes the risk of accidents to increase rapidly. Thus, it is of important practical and engineering significance to develop an efficient HPAWJF technology for soft coal seams.
Many researchers focus on the theory and practice of pressure relief and permeability enhancement of different coal seam geological conditions using the HPAWJF technology. Originally applied for breaking rocks, Hood (1976) used a water jet technology to assist drag bits in drilling hard rocks. Yazici (1989) reported that a high-pressure abrasive water jet can be used as an independent cutting tool. Li et al. (2000) found that high-pressure abrasive water jets can significantly improve both the cutting capacity and the efficiency of hard coal rock flushing. Kim (2001) examined the relationship between the volume removal rate and the rotational speed of a nozzle by using a high-pressure abrasive injection and a suspension water jet for cutting tests in hard rock. Lin et al. (2011) used numerical simulation methods and found that the cutting depth of a high-pressure abrasive jet cutter is up to 700–800 mm. Momber et al. (2011) proposed a model for the cutting of reinforced concrete members using streamline cutting tools. Lu et al. (2013) showed that the depth of a borehole drilled using a pulsating jet flushing technology can be 2.7 times deeper than using traditional flushing technology.
As noted above, the HPAWJF technology and its devices have been efficiently used for different coal seams. However, many scholars concentrate on how to evaluate and analyze the performance of the flushing technology and devices in terms of their performance, investigating parameters such as pressure, velocity, confining pressure of a water jet, structure type, wear-resistant material, nozzle diameter and type, concentration, size of abrasive, flushing time, and rock strength, etc. Because the process of flushing a coal seam for gas drainage must be completed before exploiting the coal, the permeability enhancement properties after flushing will directly affect the efficiency and safety of coal mining operation. However, the research conducted on gas drainage efficiency after flushing is rare, especially for the soft coal seams of China. Therefore, in this study, theoretical, experimental, and numerical calculations are given more attention, which have an important significance for safe and efficient operation in the coal mines of China.
In this study, numerical calculation and field experimental validation methods are employed to analyze the permeability-enhancing properties of HPAWJF in soft coal seams. To investigate the realistic failure and pressure relief processes of coal rock, coupling of the permeability and damage evolution equations is established using the theories of gas flow and coal deformation. Additionally, the gas drainage volume, tunneling speed, and coal cutting quantity of a slotted soft coal seam are analyzed. The results of this study are expected to provide fundamental information for the application of the HPAWJF technology to improve soft coal seam gas drainage and production efficiency.
Permeability Enhancement Mechanism of HPAWJF
Pressure Relief Using HPAWJF
Coal seam permeability plays a major role in the process of gas drainage from boreholes (Connell, 2009; Liu et al., 2010). For this study, stress is normally divided into three mutually perpendicular directions, as coal mass is anisotropic (Yang et al., 2011). Therefore, the effect of stress on permeability is considered to be a three-dimensional function, and the energy stored in the coal mass element is also closely related to three-dimensional stress. Moreover, according to the least energy principle (Zhao et al., 2003), the energy stored under the condition of one- or two-dimensional stress is smaller than that stored under the conditions of three-dimensional stress (Song et al., 2014).
At present, there are two major methods for flushing coal seams: horizontal radial slot and vertical circular slot (Lin and Shen, 2015). The pressure relief space is formed during water jet flushing of a borehole, which can effectively change original stress distribution and improve coal seam permeability (Shen et al., 2012). As shown in Figure 1, geostress acts on the three-dimensional space of the physical model, and the vertical circular slots are uniformly distributed in the cross section of the borehole. Three zones are formed in the area surrounding the borehole: the crushing, plastic, and elastic deformation zones (Shen et al., 2015).
The high-pressure abrasive water jet can cut a slot to a certain width and depth in a coal seam, which will reduce the three directions of force into two and lead to changes in the energy storage states of small coal mass elements surrounding the slot. As free space for the elastic recovery of the coal mass is created, the excess energy previously stored in the slotted coal mass is released (Song et al., 2014).
Under the condition of the Mohr–Coulomb criterion, the stress distribution of a circular slot (borehole) is shown in Figure 2. Here, r0 is the radius of the circular slot; R is the radius of the limit equilibrium area (Wang et al., 2012), which is much larger than the diameter of the borehole; σt is the tangential stress; σr is the radial stress; γ is the average volume of the overlying strata; and H is the depth from the surface (Wang et al., 2012). When the distance from the center of the circular slot is increased, the stress around the circular slot is also increased. At the same time, the stress at the same position is reduced, and the limit equilibrium area is extended (Shen et al., 2015).
Therefore, the use of a high-pressure abrasive water jet to cut slots in a coal seam is possible, which will change the stress state of the seam and induce the release of its internal energy. Additionally, the permeability of the slotted coal seam can be changed. In summary, mechanisms of permeability enhancement and pressure relief can be created, and the effect of HPAWJF on relief of pressure is much better than that of the conventional gas drainage method.
Coupling of Permeability and Damage Evolution in a Realistic Failure Process
Under the influence of mining, damage deformation in coal rock becomes increasingly apparent. When the stress in the mesoscopic element of a coal mass reaches a defined threshold, the element begins to deform. At the same time, the permeability of the element also changes. Based on the method of coupling of seepage and damage, coupled equations of permeability and damage evolution are established.
The elastic modulus of the damage element is defined by Formula (1):
where D is the damage variable and E0 is the elastic modulus of the non-damage element. These parameters are defined as scalar.
For uniaxial compression (Liu et al., 2015), the Mohr–Coulomb criterion is adopted in the process of element damage:
where ϕ is the internal friction angle, ϕ is the uniaxial compressive strength, σ1 is the maximum principal stress, and σ3 is the minimum principal stress.
When the stress reaches the Mohr–Coulomb damage threshold, the damage variable D can be represented as Formula (3):
where fcr is the compressive residual strength, and εc0 is the maximum compressive strain. Tang et al. (2002) demonstrated that permeability coefficient can increase rapidly in the process of damage, and the change in the permeability coefficient of the element can be represented as Formula (4):
where λ0 is the initial permeability coefficient; p is the pore pressure; and ξ, α, β are the ratios of the permeability coefficient, pore pressure coefficient, and coupling coefficient, respectively.
When the element reached the damage threshold of the uniaxial tensile strength ft,
the damage variableDcan be represented as Formula (6):
The change in the element permeability coefficient can be represented as Formula (7):
where ftr is the tensile residual strength, and ξ′ is the ratio of the permeability coefficient in the process of element damage.
Experiment and Modeling
Field Experiment
The HPAWJF system consists of a water tank, a high-pressure pump, an abrasive generator, an abrasive mixer, a flushing rod, a nozzle, and some valves and pressure gauges (Figures 3, 4). Water is pressurized by the pump, and the outflow is divided into three flow paths. In order to drive the abrasive movement, the first high-pressure water flow reaches the top of the abrasive generator. To take the abrasive away, the second high-pressure water flow through the one-way valve reaches the abrasive mixer at the bottom of the abrasive generator. To obtain an ice mixing effect, the third high pressure water flow through the bypass is directly sent to the outlet of the abrasive mixer. Then, the high-pressure abrasive water jet flows through the flushing rod and nozzle, and it slots the coal seam.
The field experiment site is the 16,071 working face of the Daping Coalmine, which is located in the western region of Henan, China. The working face is in a typical “three-soft” (soft coal, soft roof, and soft floor) coal seam. The characteristics of the seam are as follows: depth is 880 m, thickness is 1.2–1.6 m, dip angle is 4–21°, consistent coefficient of the coal is 0.2–0.6, type of coal damage is II–III, gas content of the coal seam is 15 mł/t, absolute volume of gas drainage is 1.43 mł/min, largest original gas pressure is up to 1.8 MPa, and soft coal seam thickness is 0.6 m. Before using the HPAWJF technology, the forecast indexes of outburst danger of the working face are often at the critical or above the critical state, the initial velocity of gas drainage from the borehole (q value) is 8–20 L/min, and the drilling volume (s value) is 3–5 L/m.
As shown in Figure 5, Field experiment procedures include three parts: advance preparation, flushing procedures, and monitoring of gas drainage parameters. In addition, every step is strictly monitored to ensure that the experiment is safe. The R value comprehensive index method is used to evaluate the effect of the field experiment on the critical value indexes S, q, and R (3.3, 5, and 5.3 L/m, respectively). The R value is the key index used for judging the danger of coal and gas outbursts, and the S and q values are the reference values.
Model and Parameters
To investigate the distributions of seepage and gas pressure fields in the realistic failure process of HPAWJF, numerical simulation is carried out under different coal seam permeability and flushing length conditions. Based on the actual situation of the coal mine field experiment, the initial and boundary conditions of the simulation analysis are set. The basic computational mechanics parameters of the numerical simulation model are shown in Table 1. When the permeability coefficients are 0.1 and 1, we build three models with different flushing lengths (0, 3, and 7.5 m) for the simulation, and the diameter of the slots is 50 mm. The size of the numerical model is 15 × 5 m (length × width), and the roof and floor of the model are impermeable rock.
To better protect the numerical simulation results, the mesh independence test for the model is verified using seven groups of different mesh numbers (Ding et al., 2021). In this study, a mesh number of 200,000 satisfies the requirements of computational accuracy and is selected for the model. For a satisfactory resolution in the vicinity of the interface, an H grid is constructed, and the value of y+ is approximately 10 (Figure 6; Bian et al., 2020; Zhang et al., 2021). Therefore, the mesh resolution is acceptable. Gas pressure of the working face is. 1 MPa, and internal gas pressure of the coal seam is 1.8 MPa. The numerical simulation implemented a transient process, and time step is 0.02 day.
Results and Discussion
In this section, gas pressure and gas volume distribution will be discussed under different permeability coefficient (λ). Meanwhile, gas drainage efficiency will be investigated.
The Effect of Slot Distance Under λ = 1
As shown in Figure 7A, without HPAWJF, the gas pressure relief zone is approximately 2–6 m. With the increase in the inter-distance of the coal seam, the gas pressure increased sharply. Additionally, the gas pressure decreased slowly over time. When the inter-distance of the coal seam reached 1.2 m, all of the curves exceeded the critical pressure value (0.74 MPa). At a distance of 6 m, the gas pressure did not change, and the value of the internal gas pressure of the coal seam was 1.8 MPa. That demonstrated that the effect of gas pressure relief is very limited without HPAWJF.
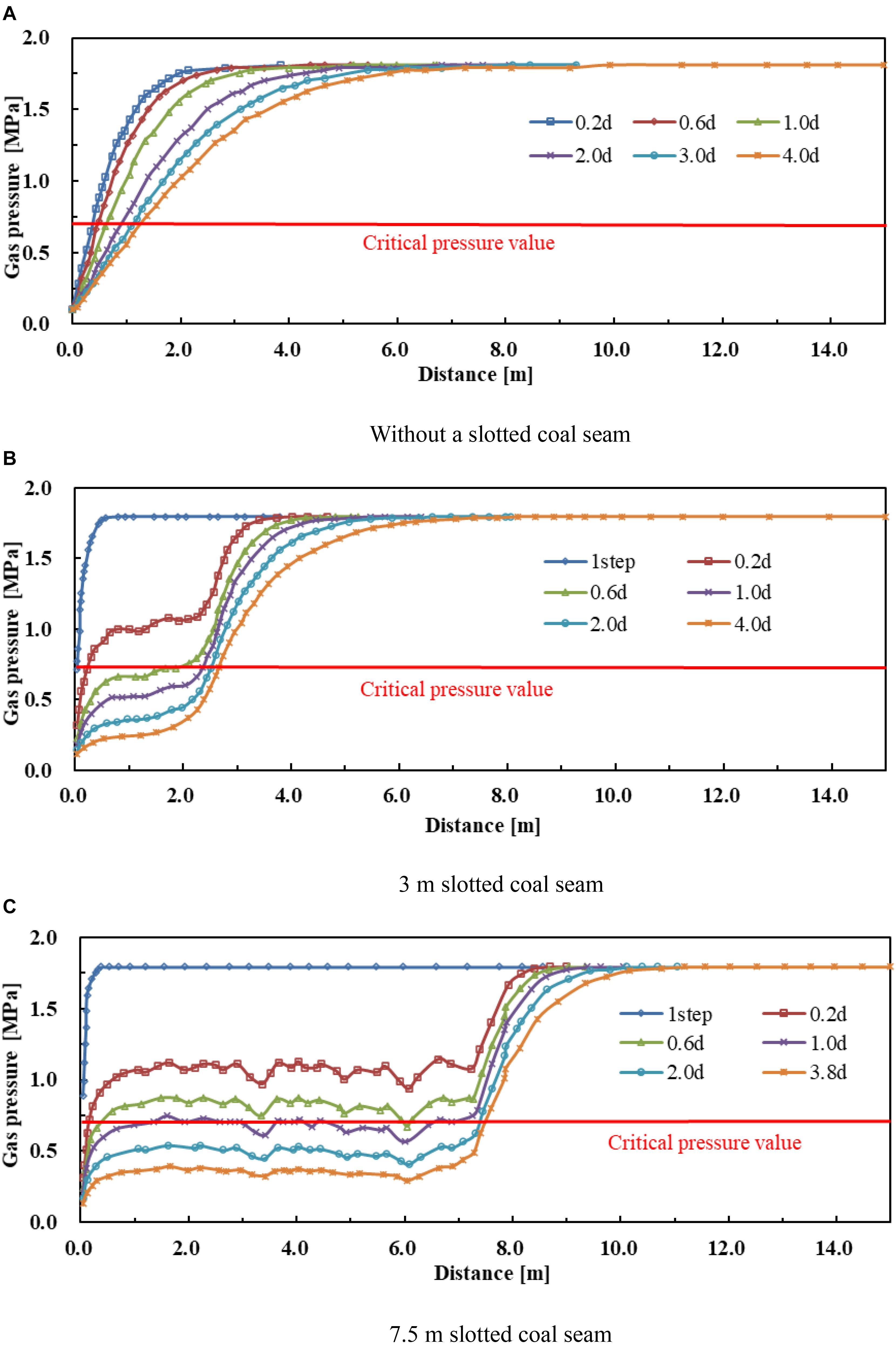
Figure 7. Variation in gas pressure: (A) without a slotted coal seam, (B) 3-m slotted coal seam, and (C) 7.5-m slotted coal seam.
To verify the effect of HPAWJF on gas pressure relief in a realistic failure process, numerical simulations using flushing lengths of 3 and 7.5 m are carried out. As shown in Figure 7B, in the slotted zone of the coal seam (0–3 m), the gas pressure changed smoothly. The maximum gas pressure relief zone increased to 6–7 m after 4 days. The curve of the gas pressure is below the critical pressure value (0.74 MPa) in the gas pressure relief zone after 0.6 day. Additionally, over time, the gas pressure decreased slowly. When the flushing length reached 2.5 m and the curve of the gas pressure increased rapidly, the internal gas pressure of the coal seam was reached. At 6–7 m, the gas pressure had no change, and the value of the internal gas pressure of the coal seam is 1.8 MPa. In the slotted zone of the coal seam (0–7.5 m) (Figure 7C), the gas pressure had little change, and the value is much lower than the others (Figures 7A,B). Over time, the gas pressure decreased. The curve of the gas pressure is below the critical pressure value (0.74 MPa) after 1 day. When the flushing length reached 7.5 m, the curve of gas pressure increased sharply and reached the internal gas pressure of the coal seam. At 10–11 m, the gas pressure had no change, and the value of the internal gas pressure of the coal seam is 1.8 MPa.
Figures 8, 9 show the gas volume fraction distributions of coal seams at different flushing lengths when the permeability coefficient is 1. In the early days of gas drainage, the gas volume fraction is very low in the slotted zones. The gas pressure relief zone increased significantly over time, and the gas volume fraction gradually became uniform in the gas drainage zone of the coal seam. Compared with the coal seam zones without flushing, the gas volume fraction decreased significantly. When the distance from the slot is increased, the gas volume fraction distribution in the coal seam is decreased, and the gas volume fraction is decreased slowly when the gas drainage time is decreased. Therefore, the desorption and diffusion of methane in the coal seam increased as a result of HPAWJF. This illustrates that the gas drainage from the coal is significantly impacted within the range of the gas pressure relief zone surrounding the center of the slot, which is consistent with the distribution of the flushing permeability enhancement function.
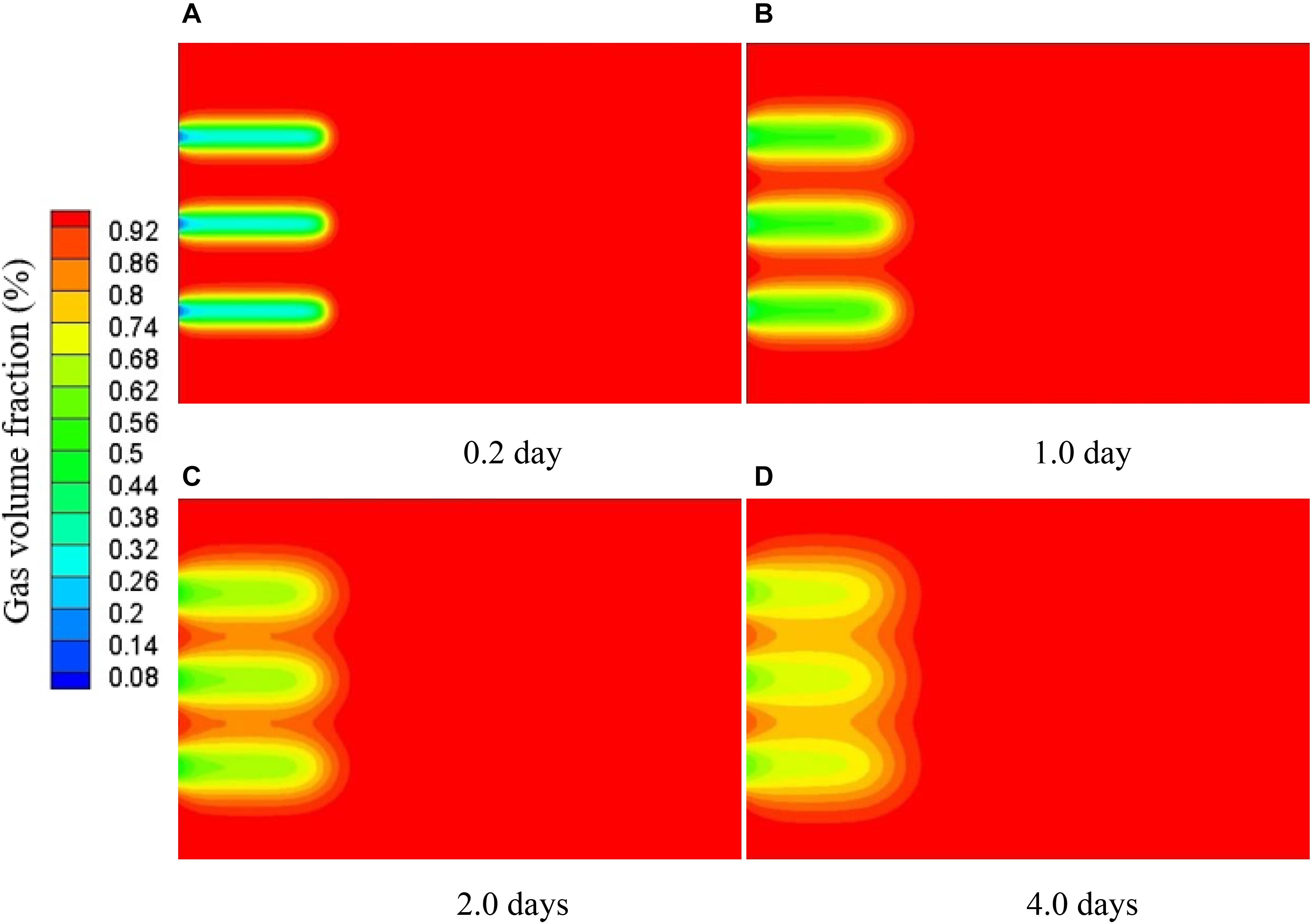
Figure 8. Gas seepage fields of a 3-m slotted coal seam when λ = 1: (A) 2 day, (B) 1 day, (C) 2 days, and (D) 4 days.
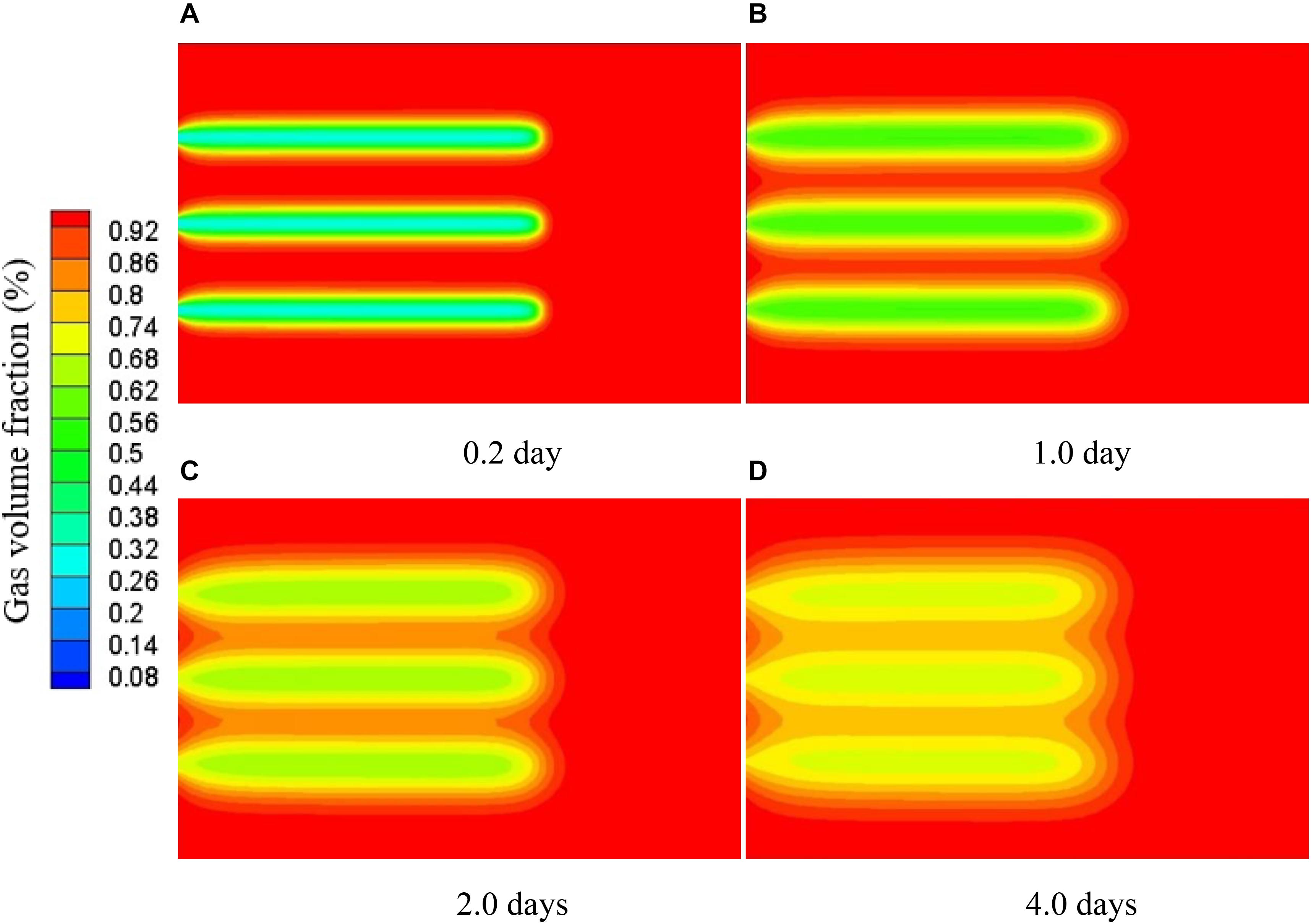
Figure 9. Gas seepage fields of a 7.5-m slotted coal seam when λ = 1: (A) 2 days, (B) 1 day, (C) 2 days, and (D) 4 days.
From Figures 7–9, it can also be observed that after 4 days of gas drainage with 3-m flushing, the average gas pressure in the zone of pressure relief is 0.319 MPa. Compared with the initial gas pressure of the coal seam it decreased by 82.3%. Similarly, after 4 days of gas drainage with 7.5-m flushing, the average gas pressure in the zone of pressure relief is 0.363 MPa, which is a 79.8% drop compared with the initial gas pressure of the coal seam. When the flushing length is increased from 3 to 7.5 m, the zone of gas pressure relief is increased synchronously.
The Effect of Slot Distance Under λ = 0.1
When the permeability coefficient is 0.1 and without HPAWJF, the gas pressure relief zone is only 2 m (Figure 10A). When the inter-distance of the coal seam is increased, the gas pressure is increased significantly. As the permeability coefficient is very low, the gas pressure of the same coal seam zone changed little over time. After 2 m, the gas pressure had no change, and the value of the internal gas pressure of the coal seam is 1.8 MPa.
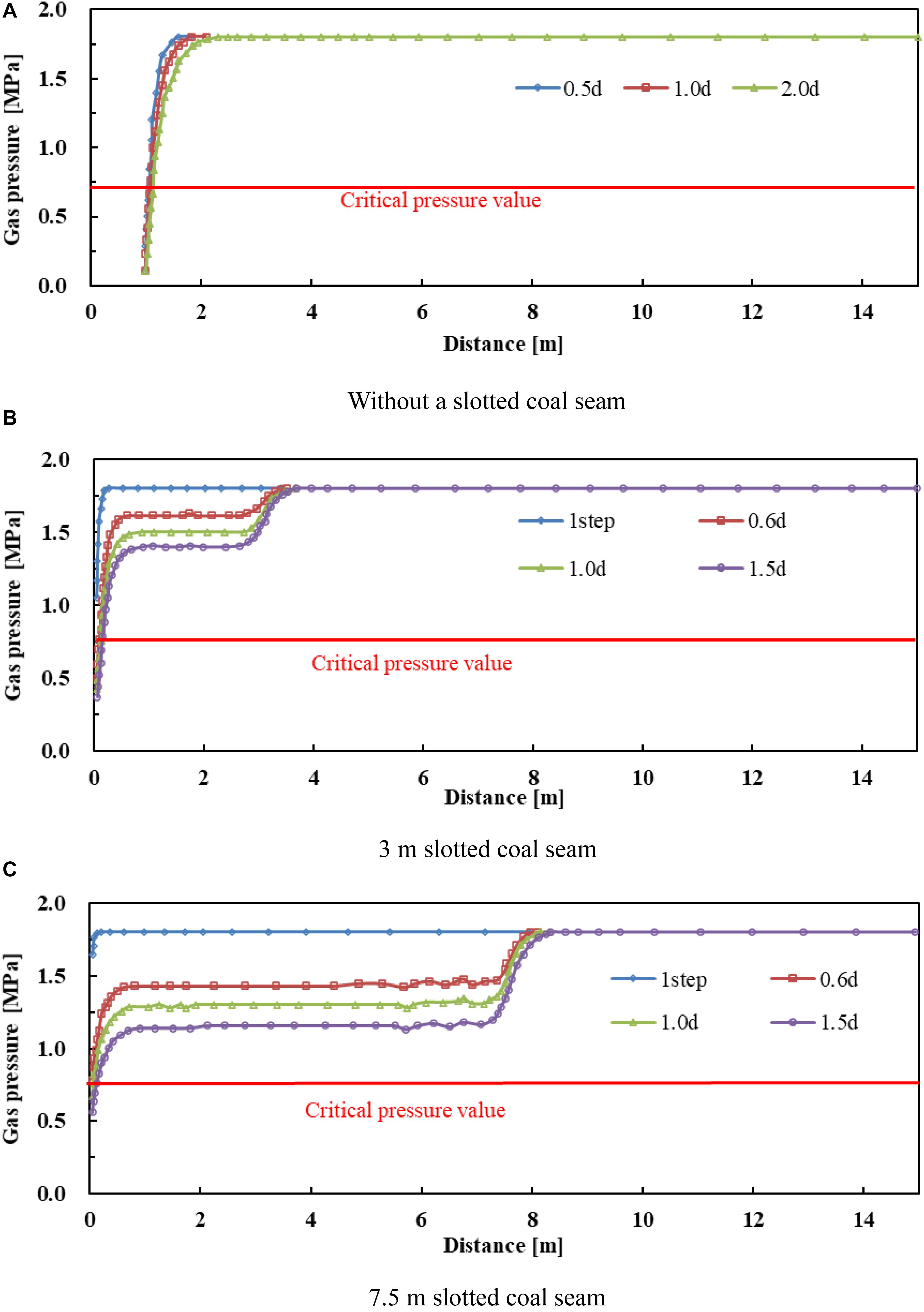
Figure 10. Variation in gas pressure: (A) without a slotted coal seam, (B) 3-m slotted coal seam, and (C) 7.5-m slotted coal seam.
As shown in Figures 10B,C, in the slotted zone of the coal seam, the gas pressure exhibited little change. The maximum gas pressure relief zone expanded to 3.5 and 8 m after 1.5 days. Additionally, over time, the gas pressure decreased slowly, and all of the curves exceeded the critical pressure value (0.74 MPa). The conclusions can be received from Figures 11 and 12 that when the flushing length reached 3 m and 7 m respectively, the curves of gas pressure increased sharply toward the internal gas pressure of the coal seam. At 3.5 and 8 m, the gas pressure had no change, and the value of the internal gas pressure of the coal seam is 1.8 MPa. Regarding the curves of the gas pressure (Figures 7, 10), although the effects of the HPAWJF permeability enhancement and pressure relief decreased significantly in lower-permeability coal seams, they are still much better than those of the conventional borehole.
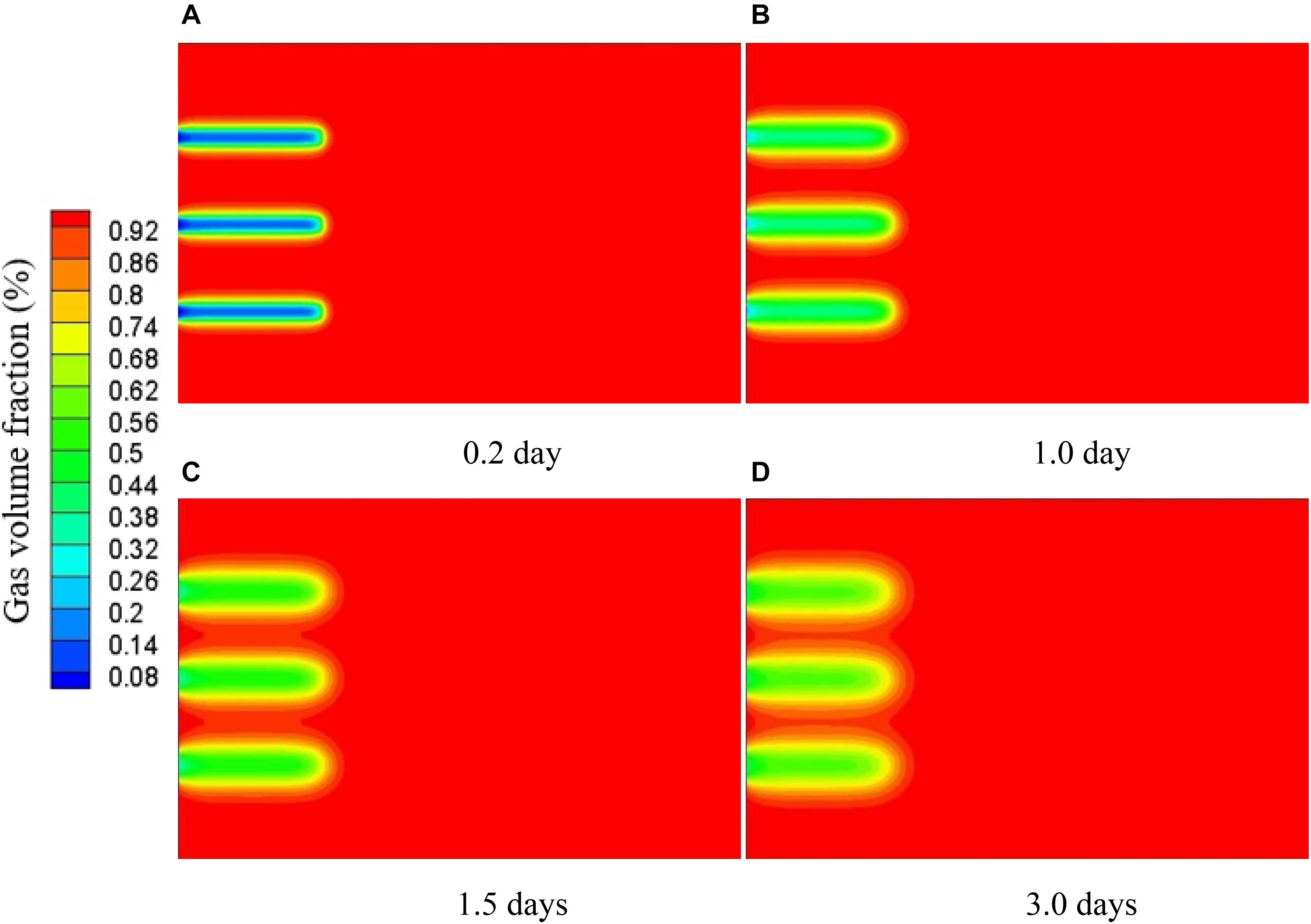
Figure 11. Gas seepage fields of a 3-m slotted coal seam when λ = 0.1: (A) 2 day, (B) 1 day, (C) 1.5 days, and (D) 3 days.
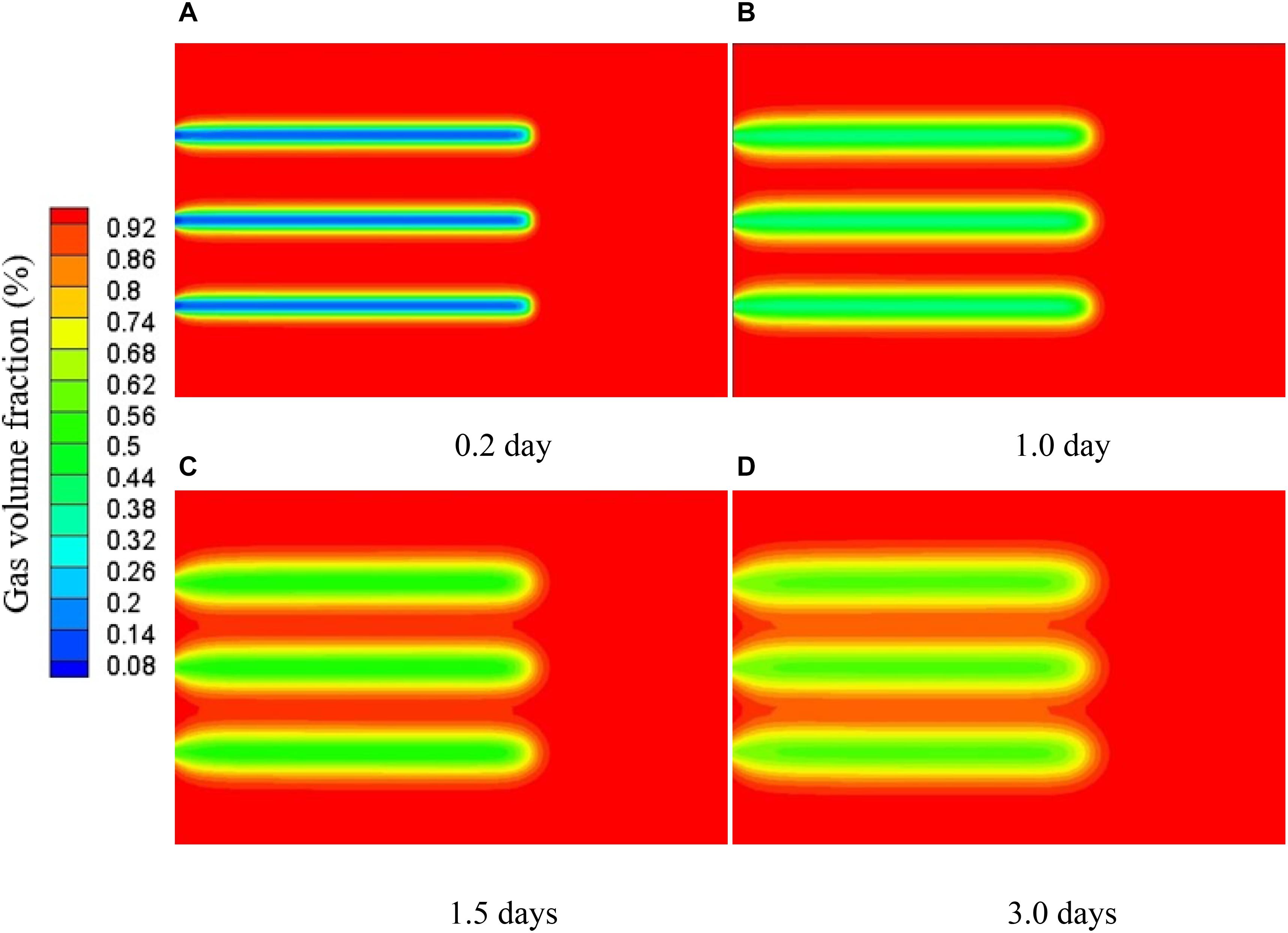
Figure 12. Gas seepage fields of a 7.5-m slotted coal seam when λ = 0.1: (A) 2 day, (B) 1 day, (C) 1.5 days, and (D) 3 days.
Because the permeability coefficient of the coal seam is lower, the applied load provided by the coal mass elements of the slot walls is insufficient to form fractures. Thus, methane desorption and diffusion of the coal seam increased marginally when HPAWJF was used. For the coal seam with lower permeability coefficient, the method of increasing the flushing length is more effective than that of increasing the gas drainage time.
Analysis of Gas Drainage Efficiency
By combining the results of the field experiment and numerical simulation, the gas drainage efficiencies of the gas drainage volume, tunneling speed, and coal cutting quantity are analyzed.
The experimental working face is a coal and gas outburst coal seam. For the pre-drainage of the gas, the conventional method for releasing holes is adopted. The value of the effective index for judging the danger of coal and gas outburst is often greater than the critical value. Using the HPAWJF technology, the initial velocity of the gas drainage from the borehole (q value) is reduced from 20 to 3.4 L/min, which indicated that the coal seam structure is damaged, leading to further changes in the internal stress of the coal mass. Thus, the scalability of the coal seam fracture net is improved, and the increase in macroporosity is conducive to the movement of gas.
For the conventional method of releasing holes, the deformation is momentary. For flushing holes, the pressure relief in the coal seam around the borehole is remarkable. Under the condition of HPAWJF, the effective stress in the coal mass is appreciably reduced, and the pressure relief zone is much larger than that of the conventional method. This shows that, in the flushing procedure, the maximum gas concentration in the roadway is 0.79%. Before flushing, the average gas concentration in the roadway is 0.21% (Figure 13). This indicates that the gas drainage volume is enhanced more than three times compared with before flushing.
In the flushing procedure, the length of each flushing cycle is 4.2 m, and the corresponding excavation time is referred to as the single cycle excavation time. The field experiment results indicated that the single-cycle excavation times before and after the use of the HPAWJF technology are 3–4 and 1–2 days, respectively. For the conventional method of releasing holes, each drilling length is 2.7–6 m, and the maximum tunneling advance length is approximately 60 m. In contrast, for the flushing holes, each flushing length of the coal seam is 4.2 m, and the maximum tunneling advance length is approximately 120 m. This demonstrated that the tunneling speed is nearly doubled compared with before.
Without using the HPAWJF technology, the tunneling advance lengths of the working face for April, May, and June are 17, 35, and 24 m, respectively (Figure 14). The average tunneling speed is 25 m/month. Using the HPAWJF technology, the tunneling advance lengths of the working face for July, August, September, October, and November are 44, 42, 44, 40, and 74 m, respectively. The average tunneling speed is 49 m/month. From the results described above, it can be concluded that the average tunneling speed increased by 96%. The experimental test results are in good agreement with the theoretical analyses.
Figure 15 shows the coal cutting quantity of each flushing cycle in a month. In the flushing process, the maximum coal cutting quantity of each flushing cycle is 6.5 t, the minimum coal cutting quantity of each flushing cycle is 3.4 t, and the average coal cutting quantity of each flushing cycle is 5.2 t. This illustrated that the abrasive water jet can directly break the coal rock and form free surfaces for the subsequent coal rock breaking procedure (Lu et al., 2013). As the quantity of coal cutting increased, increased macroporosity improved the movement of gas. These results indicated that the permeability of the coal seam had increased.
Conclusion
In this study, the results of theoretical analysis and experimental verification of pressure relief and permeability enhancement resulting from HPAWJF are presented. Based on simulations and field experiments, the distribution characteristics of seepage fields and gas pressure fields in the realistic failure process are analyzed, and gas drainage efficiencies of gas drainage volume, tunneling speed, and coal cutting quantity are correspondingly summarized. The effect of the permeability enhancement of soft coal seams is mutually verified by the results of the field experiment and numerical simulation. Conclusions from this study are as follows:
(1) The stress and energy concentration state of the coal mass could be effectively destroyed by the application of HPAWJF. The force stress propagated to deeper zones and caused the release of gas pressure from the coal seam. Thus, the pressure relief zone increased significantly. After 1.2 days of gas drainage, when the flushing length was 7.5 m, the average gas pressure of the pressure relief zone decreased to the critical pressure value (0.74 MPa). At this point, the efficiency of the gas drainage was the highest. For the lower permeability coefficient, increasing the flushing length was more effective than increasing the gas drainage time.
(2) The coal seam structure is damaged, leading to further changes in the internal stress of the coal mass. Thus, the net scalability of the coal seam fracture is improved, and the increase in macroporosity enhanced the movement of gas. The average coal cutting quantity of each flushing cycle increased to 5.2 t. The maximum gas concentration in the roadway is 0.79%. The gas drainage volume is three times higher than for conventional boreholes.
(3) The abrasive water jet could directly break the coal rock and form free surfaces for the subsequent coal rock breaking procedure, which could also force the fracture to penetrate along with the coal rock texture and to extend continuously until coal fragments are formed. When HPAWJF was used, each flushing length of the coal seam reached 4.2 m. The theoretical maximum tunneling advance length is approximately 120 m, and the maximum tunneling advance length in the field experiment is 74 m. This demonstrates that the tunneling speed is nearly two times higher than before using HPAWJF.
Data Availability Statement
The original contributions presented in the study are included in the article/supplementary material, further inquiries can be directed to the corresponding author/s.
Author Contributions
XZ and SD provided the idea. PW designed the research. PW and SD developed the literature search. XZ and GZ drafted the manuscript. All authors contributed to the article and approved the submitted version.
Conflict of Interest
The authors declare that the research was conducted in the absence of any commercial or financial relationships that could be construed as a potential conflict of interest.
Acknowledgments
Thanks are due to the support by the Postdoctoral Foundation of Henan Province (Grant No: 19030014), the China Postdoctoral Science Foundation (2019M652575), and the Science and Technology R&D Program of Henan Province of China (192102210056).
References
Aguado, M. B. D., and Nicieza, C. G. (2007). Control and prevention of gas outbursts in coal mines, riosa-olloniego coalfield, Spain. Int. J. Coal Geol. 69, 253–266. doi: 10.1016/j.coal.2006.05.004
Bian, J., Cao, X., Yang, W., Guo, D., and Xiang, C. (2020). Prediction of supersonic condensation process of methane gas considering real gas effects. Appl. Therm. Eng. 164:114508. doi: 10.1016/j.applthermaleng.2019.114508
Cao, X. W., and Bian, J. (2019). Supersonic separation technology for natural gas processing: a review. Chem. Eng. Process. 136, 138–151. doi: 10.1016/j.cep.2019.01.007
Cheng, Y. P., Wang, L., and Zhang, X. L. (2011). Environmental impact of coal mine methane emissions and responding strategies in China. Int. J. Greenh. Gas Control 5, 157–166. doi: 10.1016/j.ijggc.2010.07.007
Connell, L. D. (2009). Coupled flow and geomechanical processes during gas production from coal seams. Int. J. Coal Geol. 79, 18–28. doi: 10.1016/j.coal.2009.03.008
Ding, H., Tian, Y., Wen, C., Wang, C., and Sun, C. (2021). Polydispersed droplet spectrum and exergy analysis in wet steam flows using method of moments. Appl. Therm. Eng. 182:116148. doi: 10.1016/j.applthermaleng.2020.116148
Frid, V. (1997). Electromagnetic radiation method for rock and gas outburst forecast. J. Appl. Geophys. 38, 97–104. doi: 10.1016/s0926-9851(97)00017-7
Hood, M. (1976). Cutting strong rock with a drag bit assisted by high pressure water jets. J. S. Afr. Institute Min. Metall. 77, 79–90.
Jiang, J. Y., Cheng, Y. P., Wang, L., and Li, W. (2011). Petrographic and geochemical effects of sill intrusions on coal and their implications for gas outbursts in the Wolonghu Mine, Huaibei Coalfield, China. Int. J. Coal Geol. 88, 55–66. doi: 10.1016/j.coal.2011.08.007
Jiang, Y. D., Zhao, J. X., Liu, W. G., and Zhu, J. (2009). Investigation on the Mechanism of Coal Bumps and Relating Experiments. Beijing: Science Press.
Jin, W. C., Gao, M. Z., Yu, B., Zhang, R., Xie, J., and Qiu, Z. Q. (2015). Elliptical fracture network modeling with validation in datong mine, China. Environ. Earth Sci. 73, 7089–7101. doi: 10.1007/s12665-015-4158-4
Kim, D. I. (2001). A Study on the Cutting of Rocks by Injection type Abrasive Water Jets. M.S. Dissertation. Korea: University of Seoul National.
Li, X. H., Wang, J. S., Lu, Y. Y., Yang, L., Kang, H. M., and Sun, J. J. (2000). Experimental investigation of hard rock cutting with collimated abrasive water jets. Int. J. Rock Mech. Min. Sci. 37, 1143–1148. doi: 10.1016/s1365-1609(00)00036-8
Li, X. Z., and Hua, A. Z. (2006). Prediction and prevention of sandstone-gas outbursts in coal mines. Int. J. Rock Mech. Min. Sci. 43, 2–18. doi: 10.1016/j.ijrmms.2005.03.021
Lin, B. Q., and Shen, C. M. (2015). Coal permeability-improving mechanism of multilevel slotting by water jet and application in coal mine gas extraction. Environ. Earth Sci. 73, 5975–5986. doi: 10.1007/s12665-015-4154-8
Lin, B. Q., Meng, F. W., and Zhang, H. B. (2011). Regional gas control based on drilling–slotting–extracting integration technology. J. China Coal Soc. 36, 75–79.
Liu, J. S., Chen, Z. W., Elsworth, D., Miao, X. X., and Mao, X. B. (2010). Linking gas-sorption induced changes in coal permeability to directional strains through a modulus reduction ratio. Int. J. Coal Geol. 83, 21–30. doi: 10.1016/j.coal.2010.04.006
Liu, X. H., Dai, F., Zhang, R., and Liu, J. F. (2015). Static and dynamic uniaxial compression tests on coal rock considering the bedding directivity. Environ. Earth Sci. 73, 5933–5949. doi: 10.1007/s12665-015-4106-3
Lu, Y. Y., Tang, J. R., Ge, Z. L., Xia, B. W., and Liu, Y. (2013). Hard rock drilling technique with abrasive water jet assistance. Int. J. Rock Mech. Min. Sci. 60, 47–56. doi: 10.1016/j.ijrmms.2012.12.021
Momber, A. W., Budidharma, E., and Tjo, R. (2011). The separation of reinforced cementitious composites with a stream-line cutting tool. Resour. Conserv. Recycl. 55, 507–514. doi: 10.1016/j.resconrec.2010.12.014
Shen, C. M., Lin, B. Q., Sun, C., Zhang, Q. Z., and Li, Q. Z. (2015). Analysis of the stress–permeability coupling property in water jet slotting coal and its impact on methane drainage. J. Petrol. Sci. Eng. 126, 231–241. doi: 10.1016/j.petrol.2014.11.035
Shen, T., Wang, Y. B., Tang, D. Z., Xu, H., Lv, Y. M., He, W., et al. (2012). Dynamic variation effects of coal permeability during the coalbed methane development process in the Qinshui Basin, China. Int. J. Coal Geol. 93, 16–22. doi: 10.1016/j.coal.2012.01.006
Song, D. Z., Wang, E. Y., Liu, Z. T., Liu, X. F., and Shen, R. X. (2014). Numerical simulation of rock-burst relief and prevention by water-jet cutting. Int. J. Rock Mech. Min. Sci. 70, 318–331. doi: 10.1016/j.ijrmms.2014.05.015
Tang, C. A., Tham, L. G., Lee, P. K. K., Yang, T. H., and Li, L. C. (2002). Coupled analysis of flow, stress and damage (FSD) in rock failure. Int. J. Rock Mech. Min. Sci. 39, 477–489. doi: 10.1016/s1365-1609(02)00023-0
Wang, F. T., Ren, T., Tu, S. H., Hungerford, F., and Aziz, N. (2012). Implementation of underground longhole directional drilling technology for greenhouse gas mitigation in Chinese coal mines. Int. J. Greenh. Gas Control 11, 290–303. doi: 10.1016/j.ijggc.2012.09.006
Wang, S. L., Wu, Z. J., Guo, M. W., and Ge, X. R. (2012). Theoretical solutions of a circular tunnel with the influence of axial in situ stress in elastic-brittle-plastic rock. Tunn. Undergr. Space Technol. 30, 155–168. doi: 10.1016/j.tust.2012.02.016
Yang, W., Lin, B. Q., Qu, Y. A., Li, Z. W., Zhai, C., Jia, L. L., et al. (2011). Stress evolution with time and space during mining of a coal seam. Int. J. Rock Mech. Min. Sci. 48, 1145–1152. doi: 10.1016/j.ijrmms.2011.07.006
Yazici, S. (1989). Abrasive Jet Cutting and Drilling of Rocks. Ph.D. Dissertation. USA: University of Missouri-Rolla.
Zhang, G., Dykas, S., Majkut, M., Smofka, K., and Cai, X. (2021). Experimental and numerical research on the effect of the inlet steam superheat degree on the spontaneous condensation in the IWSEP nozzl. Int. J. Heat Mass Transf. 165:120654. doi: 10.1016/j.ijheatmasstransfer.2020.120654
Keywords: CFD, experimental study, permeability enhancement, numerical study, high-pressure abrasive water jet flushing
Citation: Zhang X, Wiśniewski P, Dykas S and Zhang G (2021) Permeability Enhancement Properties of High-Pressure Abrasive Water Jet Flushing and Its Application in a Soft Coal Seam. Front. Energy Res. 9:679623. doi: 10.3389/fenrg.2021.679623
Received: 12 March 2021; Accepted: 06 April 2021;
Published: 29 April 2021.
Edited by:
Jiang Bian, China University of Petroleum (East China), ChinaReviewed by:
Fengchao Wang, China University of Mining and Technology, ChinaZhongning Zhou, China University of Mining and Technology, China
Copyright © 2021 Zhang, Wiśniewski, Dykas and Zhang. This is an open-access article distributed under the terms of the Creative Commons Attribution License (CC BY). The use, distribution or reproduction in other forums is permitted, provided the original author(s) and the copyright owner(s) are credited and that the original publication in this journal is cited, in accordance with accepted academic practice. No use, distribution or reproduction is permitted which does not comply with these terms.
*Correspondence: Piotr Wiśniewski, piotr.wisniewski@polsl.pl; Guojie Zhang, zhangguojie2018@zzu.edu.cn